The manufacturing and engineering sectors are undergoing a significant transformation, driven by advancements in material science and precision machining. A key player in this evolution is CNC nylon, a material that offers an unparalleled combination of durability, light weight, and design flexibility. These custom-machined components are setting new standards for excellence across a multitude of industries, from automotive and aerospace to specialized industrial automation. By harnessing the power of computer numerical control (CNC) technology, raw nylon and other engineering plastics are transformed into highly precise, tailor-made parts that solve complex mechanical challenges, offering a superior alternative to traditional metal components in many high-stress applications.
The exceptional performance of these components begins with the selection of premium-grade materials. While nylon is celebrated for its remarkable durability and wear resistance, other advanced polymers like UPE (Ultra-high-molecular-weight polyethylene) and POM (Polyoxymethylene) offer specialized benefits. UPE excels in low-friction scenarios, making it ideal for sliding parts and guides, while POM provides exceptional mechanical strength and dimensional stability for load-bearing applications. This strategic use of materials ensures that every component is perfectly optimized for its intended function. This level of specialization is critical when producing high-performance parts for milling machines, where precision and resilience are non-negotiable for operational success and longevity.
The true power of this technology lies in its capacity for complete customization. Working from client drawings or existing samples, it is possible to fabricate components of virtually any shape or complexity. This process allows for the creation of everything from vibrant green gears and sleek black fasteners to intricate brackets and support structures. These are not merely replacement parts; they are often engineered improvements that can serve as the main parts of a milling machine or other complex robotic systems. The meticulous accuracy of CNC machining ensures that every gear tooth aligns perfectly and every fastener provides a secure, stable fit, guaranteeing seamless integration and peak performance within the larger assembly.
Beyond customization, the inherent properties of engineering plastics offer significant advantages over metal. These components are inherently resistant to corrosion and many chemicals, eliminating rust and degradation issues common in harsh industrial environments. Their lightweight nature reduces overall machine mass, leading to lower energy consumption and less inertia in moving parts. This is particularly valuable for essential parts for milling machines, where reduced vibration and wear can extend the life of the entire system. Furthermore, the self-lubricating properties of materials like nylon and UPE reduce the need for constant maintenance, leading to less downtime and greater operational efficiency.
The range of available materials extends even further into highly specialized polymers such as PEEK, PTFE, and UHMW. These plastics are engineered for extreme conditions, offering high-temperature resistance, superior chemical inertness, and unmatched impact strength. This versatility makes it possible to design components for the most demanding applications, including injector nozzles for fluid handling, coil spacers for electronic devices, and lightweight bearings for high-speed rotational mechanics. The ability to tailor not just the shape but also the material to the specific operational challenge unlocks a new level of innovation for engineers and designers.
In conclusion, the adoption of CNC-machined engineering plastics represents a forward-thinking approach to modern manufacturing. These components deliver a sophisticated package of precision, strength, and tailored design that pushes the boundaries of what is possible. By upgrading to these advanced solutions, including the main parts of a milling machine, companies can enhance product performance, improve reliability, and unlock new efficiencies in their operations. It is a commitment to quality and innovation that provides a distinct competitive advantage in today's fast-paced industrial landscape.
Custom CNC Nylon Components: Precision for Milling Machines
Get Latest Price >
Label | Value |
---|---|
Brand | Guangdong Engineering Plastics |
CNC Process | CNC Milling, CNC Turning, Auto lathe,Core machine, Cutting machine,Drilling Laser Cutting,etc |
Drawing format | STEP|STP|SLDPRT|JT|DXF|STL|IPT|3MF|3DXMLPRT SAT files |
Processing Equipment | CNC lathe, CNC milling machine, drilling machine |
Quanlity System | ISO 9001, RoHS Srandard, etc |
Quotation service | According to your drawing(size,material,thickness,processing content,and required technology,etc) |
Surface Treatment Tech | Polishing,Painting,Electroplate,Anodizing, Brushing, Silk Screening,Water Transfering, Leather Covering,Texture, Sanblasting,Gilding, UV Painting… |
Tolerance | +/-0.02mm |
Material | Plastic: PEEK,PPS,PTFE,POM,PE,ABS, Nylon,PC, Pvc,etc. Metal: Stainless steel, aluminum alloy, brass, steel |
Find Similar Products
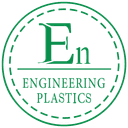
From CAD to Casting: Your Full-Service Mold & CNC Partner.
ISO 9001,SGS,FDA,ISO,CE ,ROSH,AOV Certification.
Over 100 materials available, with 50+surface finish options.
Cost-effective mass production.
Order as low as 1 piece.