In today's fast-paced industrial landscape, the demand for components that offer precision, efficiency, and durability has never been higher. Leading manufacturers of plastic parts are at the forefront of this evolution, engineering innovative solutions that outperform traditional materials. The shift from heavy, corrosion-prone metals to high-performance engineering plastics is enabling breakthroughs across numerous sectors. These advanced polymers provide a unique combination of lightweight strength, chemical resistance, and design flexibility, allowing for the creation of intricate and reliable components that drive modern machinery and automation forward. This represents a fundamental change in how engineers approach design, prioritizing efficiency without compromising on robustness.
At the core of this innovation is a diverse range of meticulously crafted components. For instance, consider racks and pinions made from engineering-grade plastics, notable for their precisely machined teeth that ensure flawless engagement and remarkably smooth, quiet operation. These are ideal for sophisticated positioning systems, automated conveyor belts, and robotic applications where noise reduction and minimal maintenance are critical. Complementing these are vibrant U-channel guide rails, engineered to provide exceptional alignment and tracking performance. Made from high-quality polymers, these guides resist high impacts, moisture, and chemical exposure, guaranteeing longevity even in the most demanding operational environments. The quality of these plastic parts sets a new standard for performance in industrial automation.
What truly sets these components apart is the intelligent design and fusion of materials. Many gears and high-stress components integrate metallic bushings at key friction points, a clever hybrid approach that enhances durability and wear resistance where it matters most. This demonstrates a deep understanding of mechanical stress and material science. These superior plastic parts are not just replacements for metal; they are purpose-built solutions designed to excel in high-stress environments, offering enhanced performance, reduced system weight, and improved energy efficiency. This thoughtful engineering ensures that every component delivers optimal functionality and a prolonged operational lifespan, contributing to more reliable and cost-effective machinery.
This commitment to excellence is evident across a wide spectrum of products, from intricately threaded adaptors and secure hex nuts to precision-molded spacers and retaining rings. Each piece is designed to provide structural integrity and seamless integration within complex assemblies. Such versatility makes them indispensable for a multitude of industries, including automotive manufacturing, aerospace engineering, and high-tech electronics. The capability of modern plastic parts factories to produce such a wide array of custom-engineered solutions empowers designers to create more efficient, compact, and innovative systems. Whether it's a cylindrical sleeve for reducing friction or a conical funnel for material handling, the right component is available to meet specific application needs.
Ultimately, this collection of advanced polymer components represents more than just an alternative to conventional materials; it embodies the future of manufacturing and engineering. By leveraging the unique properties of engineered plastics, businesses can enhance product performance, reduce operational costs, and push the boundaries of innovation. The collaboration with skilled manufacturers of plastic parts ensures that every component is crafted to the highest standards of quality and precision. Embracing this technological advancement means investing in a future where machinery is lighter, faster, quieter, and more resilient than ever before, redefining expectations for what is possible in the world of engineering.
Plastic parts factories: innovative solutions for industry
Get Latest Price >
Label | Value |
---|---|
Brand | Guangdong Engineering Plastics |
CNC Process | CNC Milling, CNC Turning, Auto lathe,Core machine, Cutting machine,Drilling Laser Cutting,etc |
Drawing format | STEP|STP|SLDPRT|JT|DXF|STL|IPT|3MF|3DXMLPRT SAT files |
Processing Equipment | CNC lathe, CNC milling machine, drilling machine |
Quanlity System | ISO 9001, RoHS Srandard, etc |
Quotation service | According to your drawing(size,material,thickness,processing content,and required technology,etc) |
Surface Treatment Tech | Polishing,Painting,Electroplate,Anodizing, Brushing, Silk Screening,Water Transfering, Leather Covering,Texture, Sanblasting,Gilding, UV Painting… |
Tolerance | +/-0.02mm |
Material | Plastic: PEEK,PPS,PTFE,POM,PE,ABS, Nylon,PC, Pvc,etc. Metal: Stainless steel, aluminum alloy, brass, steel |
Find Similar Products
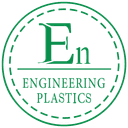
From CAD to Casting: Your Full-Service Mold & CNC Partner.
ISO 9001,SGS,FDA,ISO,CE ,ROSH,AOV Certification.
Over 100 materials available, with 50+surface finish options.
Cost-effective mass production.
Order as low as 1 piece.